FMECA
FMECA简介
故障模式、影响及危害性分析(FMECA)是针对产品所有可能的故障,并根据对故障模式的分析,确定每种故障模式对产品工作的影响,找出单点故障,并按故障模式的严酷度及其发生概率确定其危害性。所谓单点故障指的是引起产品故障的,且没有冗余或替代的工作程序作为补救的局部故障。FMECA包括故障模式及影响分析(FMEA)和危害性分析(CA)。
故障模式是指元器件或产品故障的一种表现形式。一般是能被观察到的一种故障现象。如材料的弯曲、断裂、零件的变形、电器的接触不良、短路、设备的安装不当、腐蚀等。
故障影响是指该故障模式会造成对安全性、产品功能的影响。故障影响一般可分为:对局部、高一层次及最终影响三个等级。如分析飞机液压系统中的一个液压泵,它发生了轻微漏油的故障模式,对局部即对泵本身的影响可能是降低效率,对高一层次即对液压系统的影响可能是压力有所降低,最终影响即对飞机可能没有影响。
将故障模式出现的概率及影响的严酷度结合起来称为危害性。
故障模式和影响分析(FMEA)是在产品设计过程中,通过对产品各组成单元潜在的各种故障模式及其对产品功能的影响进行分析,提出可能采取的预防改进措施,以提高产品可靠性的一种设计分析方法。它是一种预防性技术,是事先的行为,是纸上谈兵的阶段,现已从可靠性分析应用推广到产品性能分析应用上。它的作用是检验系统设计的正确性,确定故障模式的原因,及对系统可靠性和安全性进行评价等。
危害性分析(CA)是把FMEA中确定的每一种故障模式按其影响的严重程度类别及发生概率的综合影响加以分析,以便全面地评价各种可能出现的故障模式的影响。CA是FMEA的继续,根据产品的结构及可靠性数据的获得情况,CA可以是定性分析也可以是定量分析。
">编辑]FMECA的历史发展
FMECA方法最早在20世纪50年代就已经出现在航空器主操控系统之失效分析上;20世界60年代美国航天局(NASA)则成功地将FMEA应用在航天计划上;到上世纪70年代FMEA则广为汽车产业中的零件设计所应用。
FMEA在上世纪60年代已经加上严重度分析(CA)而形成FMECA方法。20世纪70年代美国汽车工业受到日本强大的竞争压力,不得不努力导入国防与航天领域应用的可靠度工程技术,以提高产品质量与可靠度,其中FMECA即为当时所导入的系统分析方法之一。经过一段时间的推广,80年代许多汽车公司已逐渐认同这项技术的成效,并开始发展、建立内部适用的FMECA技术手册,其后更将FMECA导入流程潜在失效模式之分析与改进作业中。
简言之,FMECA是藉由确定各项零件的名称,以及形成失效效应的风险衡量因子(包括可能发生失效的型式、失效发生后的后果危害性、失效本身的严重性,以及失效发生的机率和频率等项目),而判断出零件的失效状态和加以改善措施,来达到零件正常运作的标准。如果零件数很多时,必须将优先处理顺序排出来。
FMECA分析中常用的风险衡量因子为风险优先数(Risk Priority Number:RPN)。RPN由三项指标相乘构成,分别是发生度、严重度以及侦测度,即风险优先数(RPN)=发生度评分×严重度评分×侦测度评分。发生度是指某项失效原因发生之机率,其评分范围是在1-10分之间。严重度是指当失效发生时,对整个系统或是使用者影响的严重程度,其评分范围是在1-10分之间。侦测度指的是当一项零件或组件已经完成,在离开制造场所或装配场所之前,能否检测出有可能会发生失效模式的能力,评分范围在1-10分之间。
FMECA的步骤
FMECA的实施步骤通常为:
(1)掌握产品结构和功能的有关资料。
(2)掌握产品启动、运行、操作、维修资料。
(3)掌握产品所处环境条件的资料。
这些资料在设计的初始阶段,往往不能同时都掌握。开始时,只能作某些假设,用来确定一些很明显的故障模式。即使是初步FMECA,也能指出许多单点失效部位,且其中有些可通过结构的重新安排而消除。随着设计工作的进展,可利用的信息不断增多,FMECA工作应重复进行,根据需要和可能应把分析扩展到更为具体的层次。
(4)定义产品及其功能和最低工作要求。一个系统的完整定义包括它的主要和次要功能、用途、预期的性能、环境要求、系统约束条件和构成故障的条件等。由于任何给定的产品都有一个或多个工作模式,并且可能处于不同的工作阶段,因此,系统的定义还包括产品工作的每个模式及其持续工作期内的功能说明。每个产品均应有它的功能方框图,表示产品工作及产品各功能单元之间的相互关系。
(5)按照产品功能方框图画出其可靠性方框图。
(6)根据所需要的结构和现有资料的多少来确定分析级别,即规定分析到的层次。
(7)找出故障模式,分析其原因及影响。
(8)找出故障的检测方法。
(9)找出设计时可能的预防措施,以防止特别不希望发生的事件。
(10)确定各种故障模式对产品产生危害的严酷程度。
(11)确定各种故障模式的发生概率等级。
故障模式发生的概率等级一般可分为:A级(经常发生),产品在工作期间发生的概率是很高的,即一种故障模式发生的概率大于总故障概率的0.2.B级(很可能发生),产品在工作期间发生故障的概率为中等,即一种故障模式发生的概率为总故障概率的0.1—0.2.C级(偶然发生),产品在工作期间发生故障是偶然的,即一种故障模式发生的概率为总故障概率的0.01—0.1.D级(很少发生),产品在工作期间发生故障的概率是很小的,即一种故障模式发生的概率为总故障概率的0.001—0.01.E级(极不可能发生),产品在工作期间发生故障的概率接近于零,即一种故障模式发生的概率小于总故障概率的0.001.
(12)填写FMEA表,并绘制危害性矩阵,如果需要进行定量FMECA,则需填写CA表。如果仅进行FMEA,则第(11)步骤和绘制危害性矩阵不必进行。
FMECA的运用范围
FMECA(potential failure mode and effect criticality analysis)分析方法可用于整个系统到零部件任何一级,
I类(灾难性故障),它是一种会造成人员死亡或系统(如飞机)毁坏的故障。
Ⅱ类(致命性故障),这是一种导致人员严重受伤,器材或系统严重损坏,从而使任务失败的故障。
Ⅲ类(严重故障),这类故障将使人员轻度受伤、器材及系统轻度损坏,从而导致任务推迟执行、或任务降级、或系统不能起作用(如飞机误飞)。
Ⅳ(轻度故障),这类故障的严重程度不足以造成人员受伤,器材或系统损坏,但需要非计划维修或修理。
FMECA的应用">编辑]FMECA在供应链风险管理中的应用
除了采取FMECA中的发生度、严重度以及侦测度三项来衡量风险事件,本研究认为企业对于风险事件发生后的掌握能力以及复原能力也相当重要。客观的风险事件强度,可能会因为不同的风险掌控度,使得最后的结果大相径庭。因此,本研究一共采用四个因子衡量风险事件,分别为“发生可能性”、“影响程度”、“侦测程度”以及“控制程度”,而风险优先数可以定义为:RPN=(发生可能性×影响程度×侦测程度)/ 控制程度。
采用FMECA方法进行供应链风险管理,需要对常用风险管理过程各个阶段的主要任务进行一定的调整:
(1)风险识别。供应链经营过程中会遭遇的风险源可以分为五类:环境风险源、需求风险源、供应风险源、程序风险源,以及控制风险源。环境风险源分为四类:政治环境、法律环境、自然环境以及经济环境,四者合称为“总体环境”;需求风险源以及供应风险源分别以需求市场和供应市场代表,二者合称为“市场环境”;程序风险源以及控制风险源则是以“组织”、“程序”以及“控制”三方面为代表,三者合称“公司本身因素”。
风险源识别均采用问卷衡量方法,每个维度均采用五点量表,根据公司情况,针对各风险源确定相对程度。
(2)风险衡量。与传统常用风险衡量采用发生机率与潜在损失大小两个指标不同,FMECA 方法采用“发生可能性”、“影响程度”、“侦测程度”以及“控制程度”四个因子来衡量风险。
四个因子的衡量均采用5 等分方法,见下表。
风险衡量因子评分等级
(3)风险评估。根据四个风险衡量因子,可以计算出各个风险时间的风险优先系数,对这些系数进行排列,可以确定企业的主要风险关注对象。当然,风险评估是一个动态的过程,因为环境的变化会导致各个风险时间衡量因子的变化,从而影响各个风险时间的风险优先系数。例如,环境变化可能导致某些风险事件发生可能性提高或影响程度提高,从而提高该风险事件的优先级;再如,技术进步可能提高某些风险事件的控制程度,从而降低该风险事件的优先级。
(4)风险控制。传统风险控制方法强调降低风险发生可能性、减轻风险负面影响,FMECA 将侦测程度和控制程度两个因子引入风险衡量中,也扩展了风险控制的手段,即采用更为先进及时的风险侦测手段,以及改善风险控制手段。
">编辑]FMECA在食品安全追溯中的应用
将FMECA应用到食品安全可追溯性的研究中是意大利的Massimo Bertolini、Maurizio Bevilacqua和RobertoM于2003年共同提出来的。为了解决企业内部复杂的生产过程中追溯问题,他们将FMECA引入到企业内部追溯中,并提出了一个具体应用方案。
Massimo Bertolini等人通过对意大利的一家面食制品厂的案例分析,得出了可能导致企业内部追溯系统(正在设计的或已经运行的)故障的关键点,并提出了一些措施对该系统进行改进。目前,将FMECA技术应用于食品追溯链或可追溯性系统中的在国内还未见报道。
Massimo Bertolini等人进行的CA分析是选择了美军标MIL-STD-1629A中的CN法,因为具处理方法直接、数据易处理等优点。在FMECA分析过程中,他们以追溯系统的“准确”、“高效”为两个衡量指标,“故障模式”即是是指降低这两个指标的异常情况,并按严酷度和发生概率等级划分(表1)。分析结果填充在FMECA分析表单中(表2),对应的风险矩阵图(附图)中描述的各个故障模式的危害度,共分为“不可接受的”、“不欢迎的”、“偿补措施下可接受的”和“无条件接受的”4个等级。经过分析、改进、分析这样的动态过程,最终将故障模式“不可接受的”和“不欢迎的”转变为“无条件接受的”或“补偿措施下可接受的”。

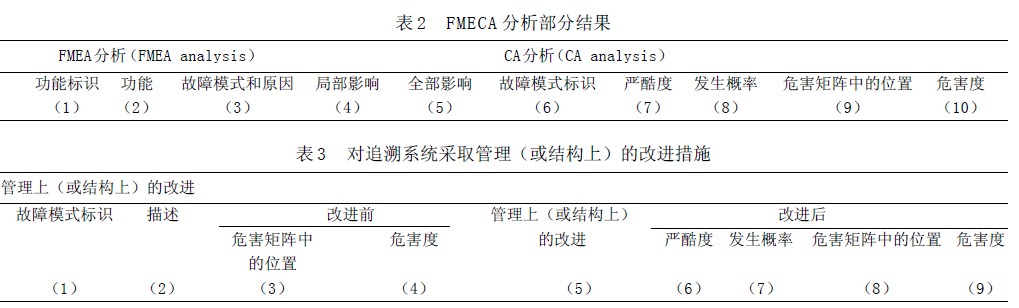
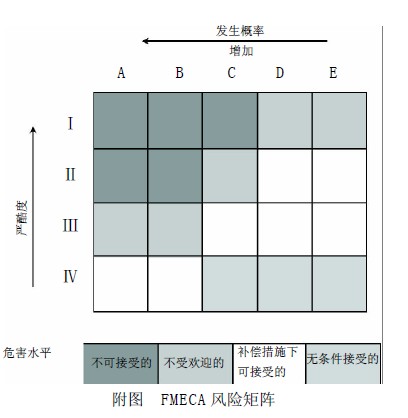
第一,定位追溯链或可追溯性系统的关键和核心问题。将FMECA应用到食品安全追溯链或可追溯性系统的分析中,根据关键点的定性(量)分析,可以识别出关键点,并提出相应的改进措施。
第二,推动可追溯性系统相关标准和规范的形成。
实现可追溯性,需要按统一的标准来管理生产、加工、包装、存储、运送和销售的各个环节。为保证可追溯系统的有效运行,利用FMECA对食品整个追溯链或可追溯性系统的分析,确定关键点(包括追溯信息、追溯方式手段等),对具有指导性的构建追溯系统的相关标准和规范的形成提供了一种方法和工具。
第三,FMECA应用效果显著、潜力大。FMECA不仅可以应用于对追溯链的某一段(或可追溯性系统的子系统)的分析,也可以应用于整个追溯链(或可追溯性系统)的分析,从而真正地实现从“农田到餐桌”的全程追溯。
FMECA在食品安全追溯链和追溯系统的研究中,需要对相关环节进行详细的分析,可能涉及到企业的内部非公开信息,企业在这些方面的开放程度较低,容易产生抵触情绪,妨碍分析工作的有效开展。目前,政府虽已经出台了一些政策,但并未有明确到位,有必要加强引导企业提高在食品安全方面的开放水平和透明度。
FMECA技术在追溯链或可追溯性系统研究工作中的应用,应该注意以下几个问题:
(1)“谁设计,谁分析”。FMECA工作应由构建追溯链和设计可追溯性系统的专门人员完成,即“谁设计、谁分析”。为了保证FMECA工作的全面性、有效性、真实性和可靠性,也可采取以设计人员为主体,吸收各方相关人员组成“FMECA团队”(如食品安全、质量控制、生产管理、物流管理等方面的人员)共同完成FMECA工作,其中可靠性专业人员应协助设计人员完成分析工作,提供实施FMECA的程序、方法,并进行适时指导。
(2)整个链的FMECA分析。通过对“从田头到餐桌”整个追溯链或可追溯性系统的FMECA分析,以全局的高度进行统筹分析,便于综合考虑各种因素(如成本、技术手段和必要性),从而准确把握和发现影响追溯链的关键节点,最终提出解决问题的方案。
(3)FMECA的动态分析过程。FMECA是一个反复迭代、逐步完善的过程。在可追溯性系统的设计和运行阶段,都可以使用FMECA分析。设计和开发完成的可追溯性系统可能并不完善,随着系统的试运行,可能会出现未曾预料的问题,还需要进行改进,而FMECA分析就可以应用到这个动态的改进过程中。
">编辑]实施FMECA应注意的问题
找出零部件所发生的故障与系统整体故障之间的因果关系是FMECA的工作思路,所以明确FMECA的分析对象,并针对其应有的功能,找出各部件可能存在的所有故障模式,是提高FMECA可靠性和有效性的前提条件。
FMEA、FMECA应与设计工作结合进行,在可靠性工程师的协助下,由产品的设计人员来完成,贯彻“谁设计、谁分析”的原则,并且分析人员必须有公正客观的态度,包括客观评价与自己有关的缺陷,理性分析缺陷的原因。同时FMEA必须与设计工作保持同步,尤其应在设计的早期阶段就开始进行FMECA,这将有助于及时发现设计中的薄弱环节并为安排改进措施的先后顺序提供依据。如果在产品已经设计完成并且已经投产以后再进行FMEA,其实对设计的指导意义不大。一旦分析出原因,就要迅速果断地采取措施,使FMEA分析的成果落到实处,而不是流于形式。
进行FMECA时,合理的分析层次确定,特别是初始约定层次和最低约定层次能够为分析提供明确的分析范围和目标或程度。此外,初始约定层次的划分直接影响到分析结果严酷度类别的确定。一般情况下,应按以下原则规定最低约定层次:。
(1)所有可获得分析数据的产品中最低的产品层次;
(2)能导致灾难的(I类)或致命的(II类)故障的产品所在的产品层次;
(3)定或预期需要维修的最低产品层次,这些产品可能导致临界的(III类)或轻度的(IV类)故障。
往往FMECA都采用个人形式进行分析的,但是单独工作无法克服个人知识、思维缺陷或者缺乏客观性。从相关领域选出具有代表性的个人,共同组成FMECA团队。通过集体的智慧,达到相互启发和信息共享,就能够较完整和全面地进行FMECA分析,大大工作效率。
FMECA特别强调程序化、文件化,并应对FMECA的结果进行跟踪与分析,以验证其正确性和改进措施的有效性,将好的经验写进企业的FMECA经验反馈里,积少成多,形成一套完整的FMECA资料,使一次次FMECA改进的量变汇集成企业整体设计制造水平的质变,最终形成独特的企业技术特色。
参考文献
故障模式、影响及危害性分析(FMECA)是针对产品所有可能的故障,并根据对故障模式的分析,确定每种故障模式对产品工作的影响,找出单点故障,并按故障模式的严酷度及其发生概率确定其危害性。所谓单点故障指的是引起产品故障的,且没有冗余或替代的工作程序作为补救的局部故障。FMECA包括故障模式及影响分析(FMEA)和危害性分析(CA)。
故障模式是指元器件或产品故障的一种表现形式。一般是能被观察到的一种故障现象。如材料的弯曲、断裂、零件的变形、电器的接触不良、短路、设备的安装不当、腐蚀等。
故障影响是指该故障模式会造成对安全性、产品功能的影响。故障影响一般可分为:对局部、高一层次及最终影响三个等级。如分析飞机液压系统中的一个液压泵,它发生了轻微漏油的故障模式,对局部即对泵本身的影响可能是降低效率,对高一层次即对液压系统的影响可能是压力有所降低,最终影响即对飞机可能没有影响。
将故障模式出现的概率及影响的严酷度结合起来称为危害性。
故障模式和影响分析(FMEA)是在产品设计过程中,通过对产品各组成单元潜在的各种故障模式及其对产品功能的影响进行分析,提出可能采取的预防改进措施,以提高产品可靠性的一种设计分析方法。它是一种预防性技术,是事先的行为,是纸上谈兵的阶段,现已从可靠性分析应用推广到产品性能分析应用上。它的作用是检验系统设计的正确性,确定故障模式的原因,及对系统可靠性和安全性进行评价等。
危害性分析(CA)是把FMEA中确定的每一种故障模式按其影响的严重程度类别及发生概率的综合影响加以分析,以便全面地评价各种可能出现的故障模式的影响。CA是FMEA的继续,根据产品的结构及可靠性数据的获得情况,CA可以是定性分析也可以是定量分析。
">编辑]FMECA的历史发展
FMECA方法最早在20世纪50年代就已经出现在航空器主操控系统之失效分析上;20世界60年代美国航天局(NASA)则成功地将FMEA应用在航天计划上;到上世纪70年代FMEA则广为汽车产业中的零件设计所应用。
FMEA在上世纪60年代已经加上严重度分析(CA)而形成FMECA方法。20世纪70年代美国汽车工业受到日本强大的竞争压力,不得不努力导入国防与航天领域应用的可靠度工程技术,以提高产品质量与可靠度,其中FMECA即为当时所导入的系统分析方法之一。经过一段时间的推广,80年代许多汽车公司已逐渐认同这项技术的成效,并开始发展、建立内部适用的FMECA技术手册,其后更将FMECA导入流程潜在失效模式之分析与改进作业中。
简言之,FMECA是藉由确定各项零件的名称,以及形成失效效应的风险衡量因子(包括可能发生失效的型式、失效发生后的后果危害性、失效本身的严重性,以及失效发生的机率和频率等项目),而判断出零件的失效状态和加以改善措施,来达到零件正常运作的标准。如果零件数很多时,必须将优先处理顺序排出来。
FMECA分析中常用的风险衡量因子为风险优先数(Risk Priority Number:RPN)。RPN由三项指标相乘构成,分别是发生度、严重度以及侦测度,即风险优先数(RPN)=发生度评分×严重度评分×侦测度评分。发生度是指某项失效原因发生之机率,其评分范围是在1-10分之间。严重度是指当失效发生时,对整个系统或是使用者影响的严重程度,其评分范围是在1-10分之间。侦测度指的是当一项零件或组件已经完成,在离开制造场所或装配场所之前,能否检测出有可能会发生失效模式的能力,评分范围在1-10分之间。
FMECA的步骤
FMECA的实施步骤通常为:
(1)掌握产品结构和功能的有关资料。
(2)掌握产品启动、运行、操作、维修资料。
(3)掌握产品所处环境条件的资料。
这些资料在设计的初始阶段,往往不能同时都掌握。开始时,只能作某些假设,用来确定一些很明显的故障模式。即使是初步FMECA,也能指出许多单点失效部位,且其中有些可通过结构的重新安排而消除。随着设计工作的进展,可利用的信息不断增多,FMECA工作应重复进行,根据需要和可能应把分析扩展到更为具体的层次。
(4)定义产品及其功能和最低工作要求。一个系统的完整定义包括它的主要和次要功能、用途、预期的性能、环境要求、系统约束条件和构成故障的条件等。由于任何给定的产品都有一个或多个工作模式,并且可能处于不同的工作阶段,因此,系统的定义还包括产品工作的每个模式及其持续工作期内的功能说明。每个产品均应有它的功能方框图,表示产品工作及产品各功能单元之间的相互关系。
(5)按照产品功能方框图画出其可靠性方框图。
(6)根据所需要的结构和现有资料的多少来确定分析级别,即规定分析到的层次。
(7)找出故障模式,分析其原因及影响。
(8)找出故障的检测方法。
(9)找出设计时可能的预防措施,以防止特别不希望发生的事件。
(10)确定各种故障模式对产品产生危害的严酷程度。
(11)确定各种故障模式的发生概率等级。
故障模式发生的概率等级一般可分为:A级(经常发生),产品在工作期间发生的概率是很高的,即一种故障模式发生的概率大于总故障概率的0.2.B级(很可能发生),产品在工作期间发生故障的概率为中等,即一种故障模式发生的概率为总故障概率的0.1—0.2.C级(偶然发生),产品在工作期间发生故障是偶然的,即一种故障模式发生的概率为总故障概率的0.01—0.1.D级(很少发生),产品在工作期间发生故障的概率是很小的,即一种故障模式发生的概率为总故障概率的0.001—0.01.E级(极不可能发生),产品在工作期间发生故障的概率接近于零,即一种故障模式发生的概率小于总故障概率的0.001.
(12)填写FMEA表,并绘制危害性矩阵,如果需要进行定量FMECA,则需填写CA表。如果仅进行FMEA,则第(11)步骤和绘制危害性矩阵不必进行。
FMECA的运用范围
FMECA(potential failure mode and effect criticality analysis)分析方法可用于整个系统到零部件任何一级,
I类(灾难性故障),它是一种会造成人员死亡或系统(如飞机)毁坏的故障。
Ⅱ类(致命性故障),这是一种导致人员严重受伤,器材或系统严重损坏,从而使任务失败的故障。
Ⅲ类(严重故障),这类故障将使人员轻度受伤、器材及系统轻度损坏,从而导致任务推迟执行、或任务降级、或系统不能起作用(如飞机误飞)。
Ⅳ(轻度故障),这类故障的严重程度不足以造成人员受伤,器材或系统损坏,但需要非计划维修或修理。
FMECA的应用">编辑]FMECA在供应链风险管理中的应用
除了采取FMECA中的发生度、严重度以及侦测度三项来衡量风险事件,本研究认为企业对于风险事件发生后的掌握能力以及复原能力也相当重要。客观的风险事件强度,可能会因为不同的风险掌控度,使得最后的结果大相径庭。因此,本研究一共采用四个因子衡量风险事件,分别为“发生可能性”、“影响程度”、“侦测程度”以及“控制程度”,而风险优先数可以定义为:RPN=(发生可能性×影响程度×侦测程度)/ 控制程度。
采用FMECA方法进行供应链风险管理,需要对常用风险管理过程各个阶段的主要任务进行一定的调整:
(1)风险识别。供应链经营过程中会遭遇的风险源可以分为五类:环境风险源、需求风险源、供应风险源、程序风险源,以及控制风险源。环境风险源分为四类:政治环境、法律环境、自然环境以及经济环境,四者合称为“总体环境”;需求风险源以及供应风险源分别以需求市场和供应市场代表,二者合称为“市场环境”;程序风险源以及控制风险源则是以“组织”、“程序”以及“控制”三方面为代表,三者合称“公司本身因素”。
风险源识别均采用问卷衡量方法,每个维度均采用五点量表,根据公司情况,针对各风险源确定相对程度。
(2)风险衡量。与传统常用风险衡量采用发生机率与潜在损失大小两个指标不同,FMECA 方法采用“发生可能性”、“影响程度”、“侦测程度”以及“控制程度”四个因子来衡量风险。
四个因子的衡量均采用5 等分方法,见下表。
风险衡量因子评分等级
(3)风险评估。根据四个风险衡量因子,可以计算出各个风险时间的风险优先系数,对这些系数进行排列,可以确定企业的主要风险关注对象。当然,风险评估是一个动态的过程,因为环境的变化会导致各个风险时间衡量因子的变化,从而影响各个风险时间的风险优先系数。例如,环境变化可能导致某些风险事件发生可能性提高或影响程度提高,从而提高该风险事件的优先级;再如,技术进步可能提高某些风险事件的控制程度,从而降低该风险事件的优先级。
(4)风险控制。传统风险控制方法强调降低风险发生可能性、减轻风险负面影响,FMECA 将侦测程度和控制程度两个因子引入风险衡量中,也扩展了风险控制的手段,即采用更为先进及时的风险侦测手段,以及改善风险控制手段。
">编辑]FMECA在食品安全追溯中的应用
将FMECA应用到食品安全可追溯性的研究中是意大利的Massimo Bertolini、Maurizio Bevilacqua和RobertoM于2003年共同提出来的。为了解决企业内部复杂的生产过程中追溯问题,他们将FMECA引入到企业内部追溯中,并提出了一个具体应用方案。
Massimo Bertolini等人通过对意大利的一家面食制品厂的案例分析,得出了可能导致企业内部追溯系统(正在设计的或已经运行的)故障的关键点,并提出了一些措施对该系统进行改进。目前,将FMECA技术应用于食品追溯链或可追溯性系统中的在国内还未见报道。
Massimo Bertolini等人进行的CA分析是选择了美军标MIL-STD-1629A中的CN法,因为具处理方法直接、数据易处理等优点。在FMECA分析过程中,他们以追溯系统的“准确”、“高效”为两个衡量指标,“故障模式”即是是指降低这两个指标的异常情况,并按严酷度和发生概率等级划分(表1)。分析结果填充在FMECA分析表单中(表2),对应的风险矩阵图(附图)中描述的各个故障模式的危害度,共分为“不可接受的”、“不欢迎的”、“偿补措施下可接受的”和“无条件接受的”4个等级。经过分析、改进、分析这样的动态过程,最终将故障模式“不可接受的”和“不欢迎的”转变为“无条件接受的”或“补偿措施下可接受的”。

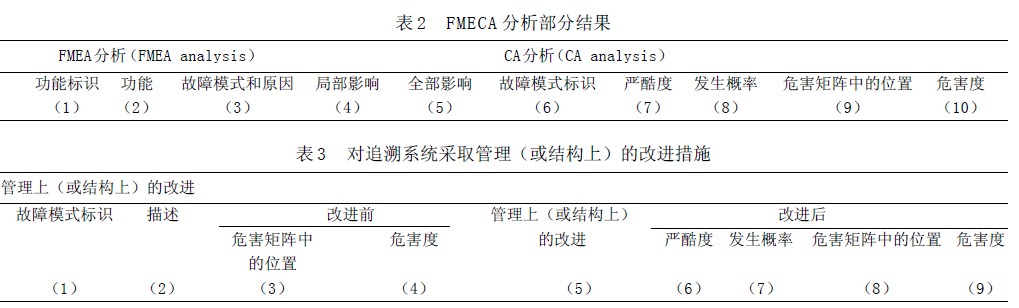
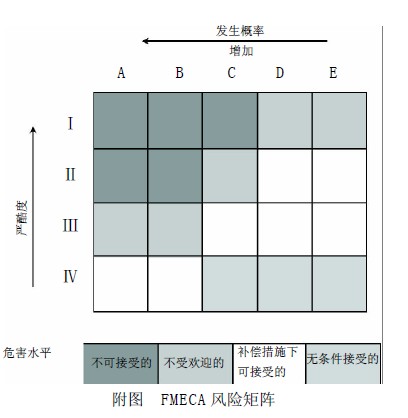
- 小结
- 将FMECA应用到食品追溯链或可追溯性系统中,至少有以下几点意义:
第一,定位追溯链或可追溯性系统的关键和核心问题。将FMECA应用到食品安全追溯链或可追溯性系统的分析中,根据关键点的定性(量)分析,可以识别出关键点,并提出相应的改进措施。
第二,推动可追溯性系统相关标准和规范的形成。
实现可追溯性,需要按统一的标准来管理生产、加工、包装、存储、运送和销售的各个环节。为保证可追溯系统的有效运行,利用FMECA对食品整个追溯链或可追溯性系统的分析,确定关键点(包括追溯信息、追溯方式手段等),对具有指导性的构建追溯系统的相关标准和规范的形成提供了一种方法和工具。
第三,FMECA应用效果显著、潜力大。FMECA不仅可以应用于对追溯链的某一段(或可追溯性系统的子系统)的分析,也可以应用于整个追溯链(或可追溯性系统)的分析,从而真正地实现从“农田到餐桌”的全程追溯。
FMECA在食品安全追溯链和追溯系统的研究中,需要对相关环节进行详细的分析,可能涉及到企业的内部非公开信息,企业在这些方面的开放程度较低,容易产生抵触情绪,妨碍分析工作的有效开展。目前,政府虽已经出台了一些政策,但并未有明确到位,有必要加强引导企业提高在食品安全方面的开放水平和透明度。
FMECA技术在追溯链或可追溯性系统研究工作中的应用,应该注意以下几个问题:
(1)“谁设计,谁分析”。FMECA工作应由构建追溯链和设计可追溯性系统的专门人员完成,即“谁设计、谁分析”。为了保证FMECA工作的全面性、有效性、真实性和可靠性,也可采取以设计人员为主体,吸收各方相关人员组成“FMECA团队”(如食品安全、质量控制、生产管理、物流管理等方面的人员)共同完成FMECA工作,其中可靠性专业人员应协助设计人员完成分析工作,提供实施FMECA的程序、方法,并进行适时指导。
(2)整个链的FMECA分析。通过对“从田头到餐桌”整个追溯链或可追溯性系统的FMECA分析,以全局的高度进行统筹分析,便于综合考虑各种因素(如成本、技术手段和必要性),从而准确把握和发现影响追溯链的关键节点,最终提出解决问题的方案。
(3)FMECA的动态分析过程。FMECA是一个反复迭代、逐步完善的过程。在可追溯性系统的设计和运行阶段,都可以使用FMECA分析。设计和开发完成的可追溯性系统可能并不完善,随着系统的试运行,可能会出现未曾预料的问题,还需要进行改进,而FMECA分析就可以应用到这个动态的改进过程中。
">编辑]实施FMECA应注意的问题
- 1.明确分析对象
找出零部件所发生的故障与系统整体故障之间的因果关系是FMECA的工作思路,所以明确FMECA的分析对象,并针对其应有的功能,找出各部件可能存在的所有故障模式,是提高FMECA可靠性和有效性的前提条件。
- 2.时间性
FMEA、FMECA应与设计工作结合进行,在可靠性工程师的协助下,由产品的设计人员来完成,贯彻“谁设计、谁分析”的原则,并且分析人员必须有公正客观的态度,包括客观评价与自己有关的缺陷,理性分析缺陷的原因。同时FMEA必须与设计工作保持同步,尤其应在设计的早期阶段就开始进行FMECA,这将有助于及时发现设计中的薄弱环节并为安排改进措施的先后顺序提供依据。如果在产品已经设计完成并且已经投产以后再进行FMEA,其实对设计的指导意义不大。一旦分析出原因,就要迅速果断地采取措施,使FMEA分析的成果落到实处,而不是流于形式。
- 3.层次性
进行FMECA时,合理的分析层次确定,特别是初始约定层次和最低约定层次能够为分析提供明确的分析范围和目标或程度。此外,初始约定层次的划分直接影响到分析结果严酷度类别的确定。一般情况下,应按以下原则规定最低约定层次:。
(1)所有可获得分析数据的产品中最低的产品层次;
(2)能导致灾难的(I类)或致命的(II类)故障的产品所在的产品层次;
(3)定或预期需要维修的最低产品层次,这些产品可能导致临界的(III类)或轻度的(IV类)故障。
- 4.FMECA团队协作和经验积累
往往FMECA都采用个人形式进行分析的,但是单独工作无法克服个人知识、思维缺陷或者缺乏客观性。从相关领域选出具有代表性的个人,共同组成FMECA团队。通过集体的智慧,达到相互启发和信息共享,就能够较完整和全面地进行FMECA分析,大大工作效率。
FMECA特别强调程序化、文件化,并应对FMECA的结果进行跟踪与分析,以验证其正确性和改进措施的有效性,将好的经验写进企业的FMECA经验反馈里,积少成多,形成一套完整的FMECA资料,使一次次FMECA改进的量变汇集成企业整体设计制造水平的质变,最终形成独特的企业技术特色。
参考文献
- ↑ 1.0 1.1 张进发.FMECA方法在供应链风险管理中的应用研究.物流技术.2009年03期
- ↑ 李春华 刘世洪 郭波莉 朱海鹏.FMECA在食品安全追溯中的应用现状分析.中国食物与营养.2008年06期
- ↑ 杨兰清 林秀兰.FMECA应用中主要问题的探讨.黑龙江科技信息.2009年24期
附件列表
词条内容仅供参考,如果您需要解决具体问题
(尤其在法律、医学等领域),建议您咨询相关领域专业人士。